The concept of lean administration provides effective methods for optimizing processes and structures in indirect areas of the company.
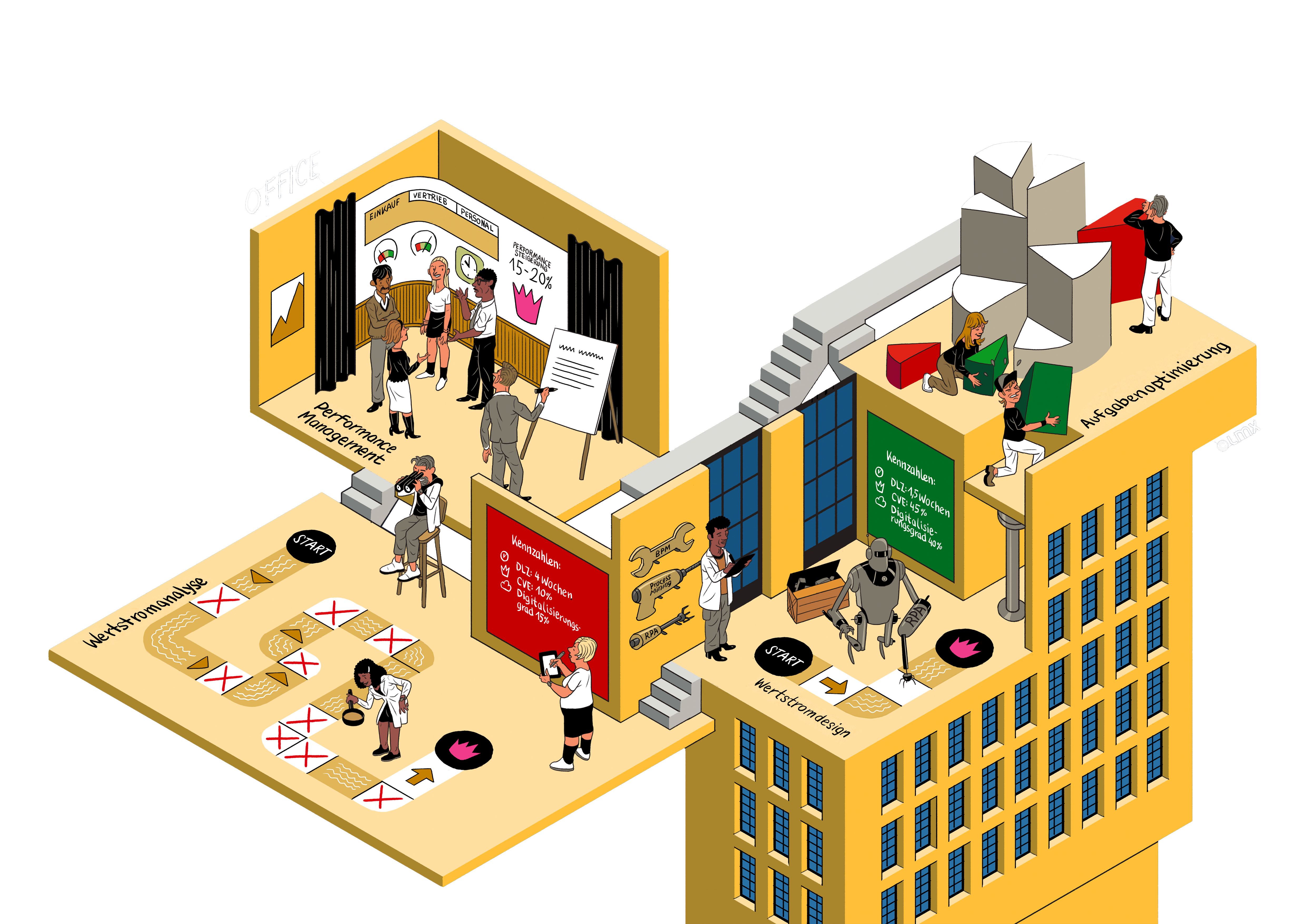
Lean Administration
The concept of lean administration provides effective methods for optimizing processes and structures in indirect areas of the company.
Processes and structures in indirect areas have enormous potential for increasing value. Analyses show that almost half of the available time is "wasted" - bad processes and historically grown structures lead to this result.
Lean Administration helps to identify the waste, to make performance visible and to increase the added value in processes and structures in the long term - with a consistent focus on (internal) customer needs. The analysis and optimization of information flows contribute significantly to the target image of the Lean Company. With Lean Administration, it is possible to digitize in a meaningful way and automate in a targeted manner with the focus on people.
Typical types of waste in administration, office and information flows
- Over-information, too much information, unnecessary meetings & emails, blind services
- Backlogs, unprocessed open items, emails, procedures
- Travel activities, travel times
- Waiting times
- Redundant activities
- Media disruptions
- Lack of IT systems, isolated applications
- Queries and rework
- Incorrect deployment of employees
- Unused knowledge and skills
Typical results of Lean Administration
- Increase in productivity / efficiency
- Reduction of lead time
- Reduction of interfaces
- Increase in delivery reliability
- Improvement of transparency and communication
- Increase of internal and external customer satisfaction
- Improvement of employee satisfaction
Get started immediately with our LMX Lean Barometer
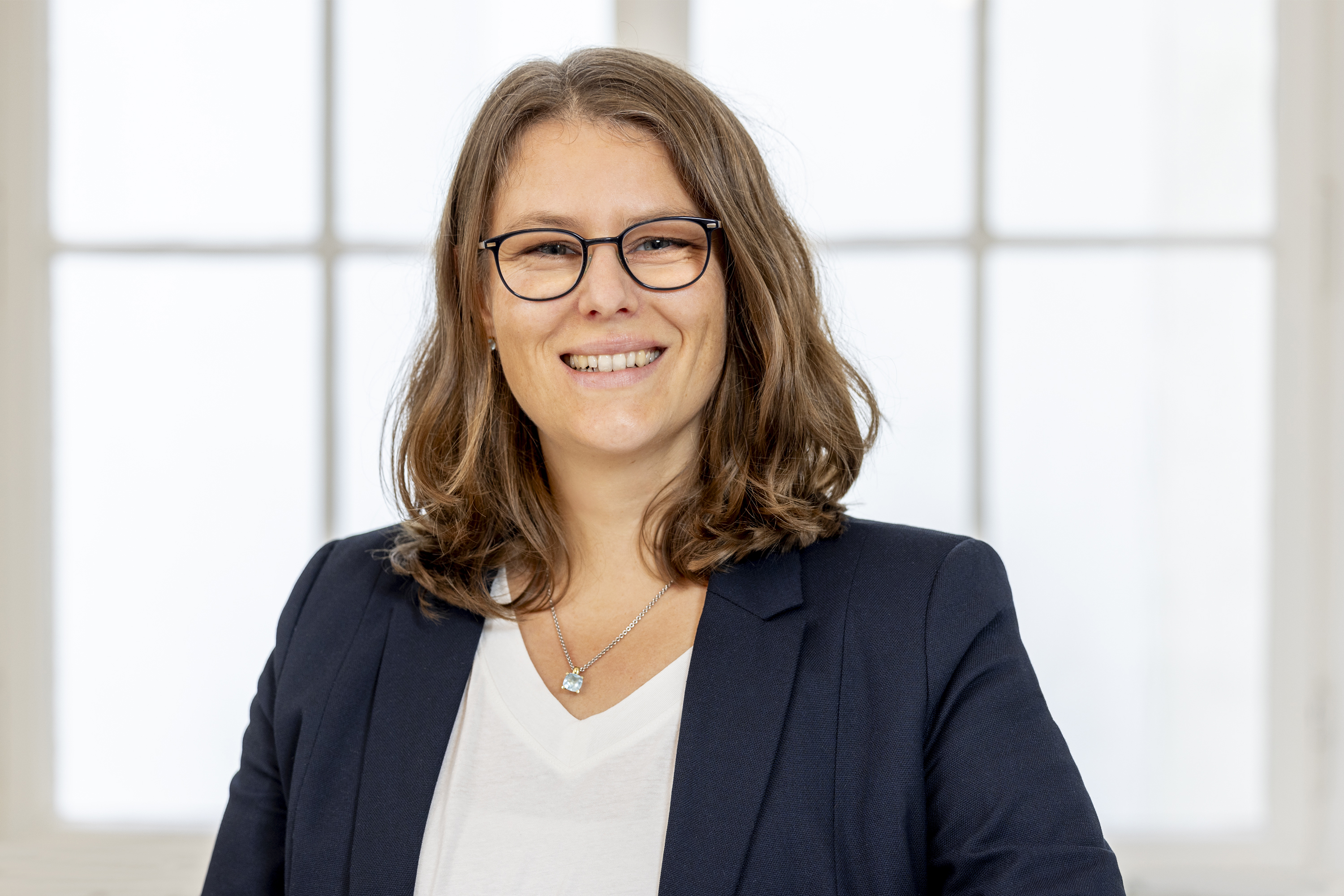
Judith Fellsches
Managing Partner
Phone: +49 211 63 55 89 60
Fax: +49 211 63 55 89 69
Email: info@lmx.eu
Lean Management & Digitization 2025 at Ruhr-University Bochum
Our solutions
Value Stream Analysis and Design / Process Mapping
"Who does what?" is one of many questions answered in value stream mapping. Processes are analyzed, optimized and implemented using a proven approach.
Target: Create transparency and waste-free processes
Value Stream Analysis and Design / Process Mapping
"Who does what?" is one of many questions answered in value stream mapping. Processes are analyzed, optimized and implemented using a proven approach.
Target: Create transparency and waste-free processes
Officefloor Management
The visualization of processes, key figures and task distribution is an important element in office floor management. The product information is invisible and visualization is therefore crucial.
Target: Target-oriented management and control
Task optimization
We analyze how much time is spent on which tasks and increase value-added time by reducing waste. The analysis is done conveniently with the help of the LMX app.
Target: Transparency, creating free space for additional value creation.
Digitize and Automate with BPM, Process Mining and RPA
We analyze and optimize your processes with the help of Business Process Management, Process Mining and RPA. Meaningful digitalization and automation complement value stream mapping and design. Here we follow the motto "First optimize then automate".
Target: Optimization by means of digitalization and automation
Potential analysis
We identify improvement potentials through a mix of Lean methods and evaluate them. Through a joint quantification in the team, the acceptance and implementation probability is increased.
Target: Quantified and qualitative improvement measures
Performance Management
Making the performance of an area, department, or process visible is the first step of the approach. The consistent orientation towards metrics with target values and the processing of deviations are the target.
Target: Key figure-oriented management and control
Value Process Management
From one-time process optimization to continuous and systematic process management - we help to set up the necessary structures, roles and IT tools.
Target: Measurable, systematic and continuous process optimization